BallFinishNose – Crank Shaft – AH715
IMPROVED PRODUCTIVITY AND TOOL LIFE
The conventional product used a solid ball end mill for chamfering the holes in the crankshaft.
Due to the large chamfer width of 1.2 mm, chatter easily occurred in this process. For this process, we proposed a two-flute insert-type ball end mill.
The reduction in the number of flutes from four in the conventional product to two helped suppress the occurrence of chatter. Additionally, the switch to an insert-type tool reduced the unit price of the tool, cutting tool costs in half.
Share
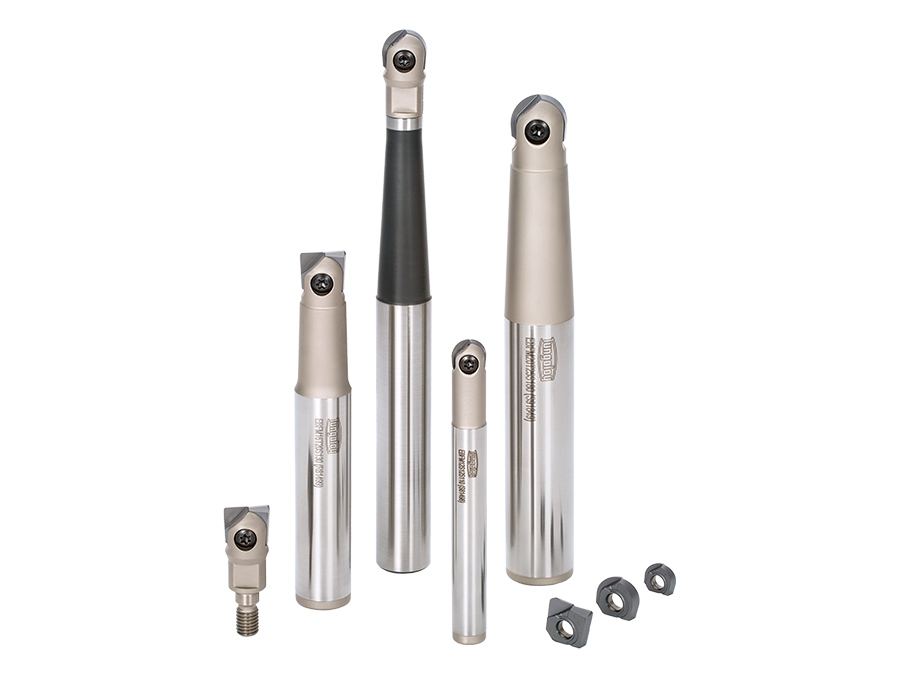
Industry | Automotive |
---|---|
Component | Crank Shaft |
Material ISO code |
|
Work material | S45C/C45 |
Machine(spindle type) | Vertical Machining Center Small(#30,HSK40) |
Tool family | Milling |
Tool category | Chamfering |
Product name | BallFinishNose |
TSR No. | 5034M |
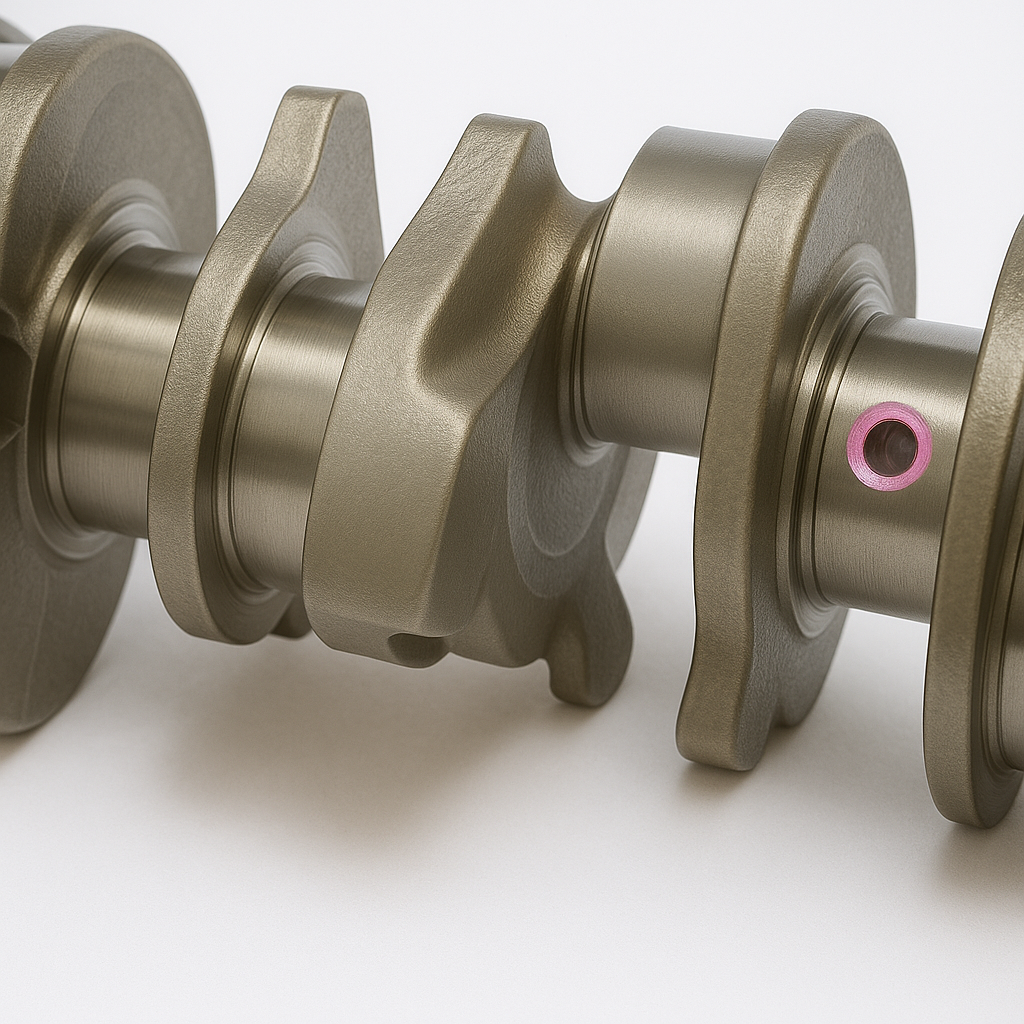
Tool
Tungaloy | Competitor | |
---|---|---|
Body | EBFM12S12S110 | Solid ball endmill |
Effective number of teeth | 2 | 4 |
Cutting diameter | 12 | 12 |
Insert | ZFBM120R00MJ | |
Number of cutting edges | 1 | 1 |
Grade | AH710 | PVD |
Cutting conditions
Tungaloy | Competitor | |
---|---|---|
Cutting speed V/c (m/min) | 40 | 27 |
Feed per tooth f/z (mm/t) | 0.04 | 0.026 |
Feed speed Vf (mm/min) | 85 | 75 |
Depth of cut ap (mm) | 1.5 | 1.5 |
Coolant | Dry | Dry |